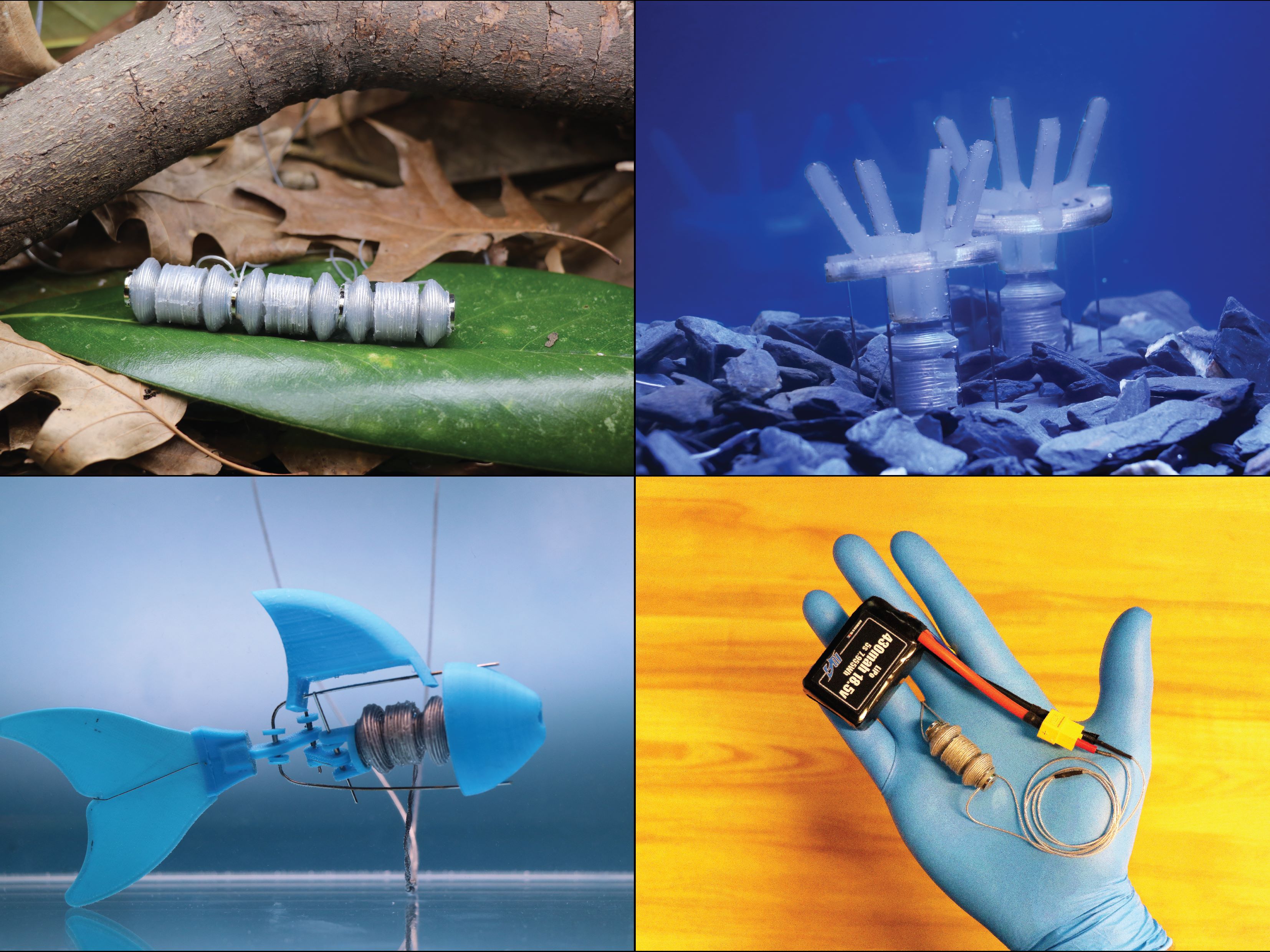
Self-Regulating Soft Oscillators Enable Battery-Powered Motion in Soft Robots
May 12, 2025
By Chloe Arrington
Soft robots are known for their flexibility and adaptability, but most still rely on rigid electronic components for control and timing. A recent publication from researchers at Georgia Tech challenges that paradigm.
Noah Kohls, Ph.D. ME 2024, and Ellen Yi Chen Mazumdar, assistant professor in the George W. Woodruff School of Mechanical Engineering, recently published a new study featured on the cover of Advanced Materials Technologies. The paper describes the development of the first self-regulating soft electromagnetic oscillators. These actuators are also the first to operate using only a battery—no external microcontrollers, pumps, or logic circuits are required.
"We wanted to design a soft system that could perform realistic tasks while being fully self-contained," said Kohls. "By embedding control into the structure itself, we reduce the need for bulky, rigid electronics."
The team's approach draws from both biology and traditional electromechanical systems. Inspired by the peristaltic motion of earthworms, the researchers developed soft linear and rotary actuators capable of producing complex motion through a combination of silicone structures, custom-compliant magnets, and liquid metal conductors. These actuators can perform various tasks, including driving a robotic car, running a fan, actuating a pump, and propelling underwater while remaining flexible and deformable.
This new class of soft electromagnetic oscillators can produce rhythmic motion and coordination, similar to how a clock regulates timing in traditional systems. These oscillators allow soft robots to move—by crawling, hopping, or swimming—using only a low-voltage power source (5 to 20 volts) and achieving higher frequencies (20 to 40 hertz) than comparable soft actuators.
These forms of movement could be helpful in applications in navigating dynamic environments where compliance and a small form factor are necessary, such as inside the human body.
"My goal was to create a soft, power-efficient, and self-contained system capable of complex locomotion and autonomous operation, ideal for applications in robotics, haptics, and medical devices," said Kohls.
Kohls' interest in robotics began while working on his undergraduate senior capstone project, during which he designed and built a custom robot to help his family's plant nursery, Firehouse Nursery. Every spring, they would plant over 10,000 cuttings by hand, and Kohls saw the opportunity to combine his love for plants and fascination for automation by making a robot that could help the business.
"That early project showed me the power of robotics to improve everyday tasks," said Kohls. "Now I'm excited to work on systems that could one day improve lives in even more impactful ways."